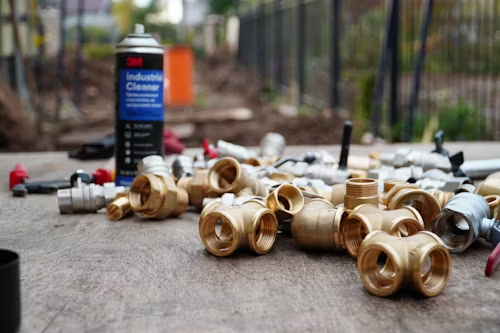
Welded fittings are a critical component in the assembly of piping systems, especially in heavy industries such as oil and gas, chemical manufacturing, and power generation. These fittings ensure the safe and efficient transport of fluids, gases, and semi-solids under high pressure and temperature conditions. This article explores the various applications and advantages of welded fittings in heavy industries, highlighting how they contribute to the robustness and reliability of industrial operations in Malaysia.
Key Applications in Heavy Industry
Oil and Gas: Welded fittings are extensively used in the oil and gas industry for constructing pipelines that transport crude oil, natural gas, and processed products. Their ability to withstand high pressures and corrosive environments makes them ideal for offshore and onshore installations.
Chemical Manufacturing: In chemical plants, welded fittings are essential for systems that carry aggressive chemicals. They provide a secure and leak-proof connection, preventing hazardous spills and exposure to potentially dangerous substances.
Power Generation: They are used in power plants for steam distribution, cooling water systems, and feedwater lines. They play a vital role in maintaining the integrity of systems that are critical to the generation of power.
Advantages of Welded Fittings
Durability and Strength: It offers exceptional durability and strength, which are necessary attributes in heavy industrial settings. The welding process creates a permanent bond that is often stronger than the base metal, ensuring that the joint can handle stress and thermal cycling without failure.
Leak Resistance: A major advantage of the fittings is their ability to provide a tight seal. Welded joints are less prone to leaks compared to non-welded connections, such as threaded or flanged fittings, making them safer and more reliable for transporting hazardous or high-pressure materials.
Cost-Effectiveness: Although the initial cost of welding can be high due to the skill and equipment required, welded fittings are more cost-effective in the long run. They require less maintenance and have a longer lifespan than other types of fittings, reducing the overall lifecycle cost of the piping system.
Customization: Welded fittings can be custom fabricated to meet specific requirements, which is particularly useful in heavy industries where standard fittings may not suffice. Custom welding allows for the creation of fittings that perfectly match the geometry and specifications of the system they will be used in.
Considerations for Effective Use
Quality of Workmanship: The effectiveness of welded fittings greatly depends on the quality of the welding job. It is crucial to employ certified welders and follow stringent welding procedures to ensure the integrity of the welds.
Inspection and Testing: Regular inspection and testing are necessary to maintain the safety and efficiency of welded fittings. Techniques such as radiographic, ultrasonic, and magnetic particle inspection are used to detect any imperfections or weaknesses in welds.
Material Compatibility: Choosing the right material for welded fittings is essential to prevent issues such as galvanic corrosion. The materials of the pipes and fittings must be compatible with each other and with the substances being transported.
Conclusion
Welded fittings are indispensable in heavy industry, offering robust, reliable, and safe solutions for complex and demanding applications. Their strength, leak resistance, and cost-effectiveness make them a preferred choice for industries that cannot afford compromises in system integrity. By adhering to high standards of installation and maintenance, industries can fully leverage the benefits of the fittings to enhance their operations.